In international trade, the export transportation of hazardous materials (dangerous goods) is strictly regulated to ensure safety during transport. Many companies ask, “Is it necessary to use a dangerous goods warehouse for packing when exporting hazardous materials?” The answer is: in most cases, it is required, but not absolutely. It specifically depends on the qualifications and operational capabilities of the company.
Why do most hazardous materials exports need to go through a hazardous materials warehouse ?
1. Regulatory Requirements
The export of hazardous materials involves “Hazardous Chemicals Export Declaration” and must meet the following core conditions:
- Storage facilities with hazardous materials storage qualifications (ordinary warehouses do not meet regulatory requirements).
- Professional packer facial recognition + location tracking + packing photos (to ensure compliance during the packing process).
- Valid dangerous goods certificate (proving that packaging meets international transport standards).
Due to the fact that most foreign trade enterprises or factories do not have the qualifications for hazardous materials storage and packing, they usually entrust professional hazardous materials warehouses for internal packing.
2. Safety and Risk Management
- The hazardous materials warehouse is equipped with explosion-proof, fireproof, and leak-proof facilities to reduce accident risks.
- Professional packers are familiar with international regulations such as IMDG (maritime) and IATA (air), ensuring compliance in packing.
- Avoid customs inspections, re-shipments, or fines due to improper handling.
Under what circumstances can interior work be done without being in a hazardous materials warehouse ?
Although most companies need to pack dangerous goods in a hazardous materials warehouse, the following situations may be exceptions:
1. The factory has been registered with the Maritime Bureau.
If the factory has obtained registration for packing dangerous goods from the Maritime Bureau and possesses:
- Own packing staff (must hold a certificate to work).
- EDI system (can send packing information to customs/shipping companies).
- Storage area for hazardous materials that meets standards.
The packaging can be completed within the factory, but complete declaration materials (such as hazardous goods certificates) are still required.
2. Some low-risk hazardous materials (depending on the situation)
Certain low-hazard goods (such as some chemical products with UN numbers) may be allowed to be packed in locations that meet safety standards, but it is still necessary to consult with freight forwarders or maritime authorities for confirmation.
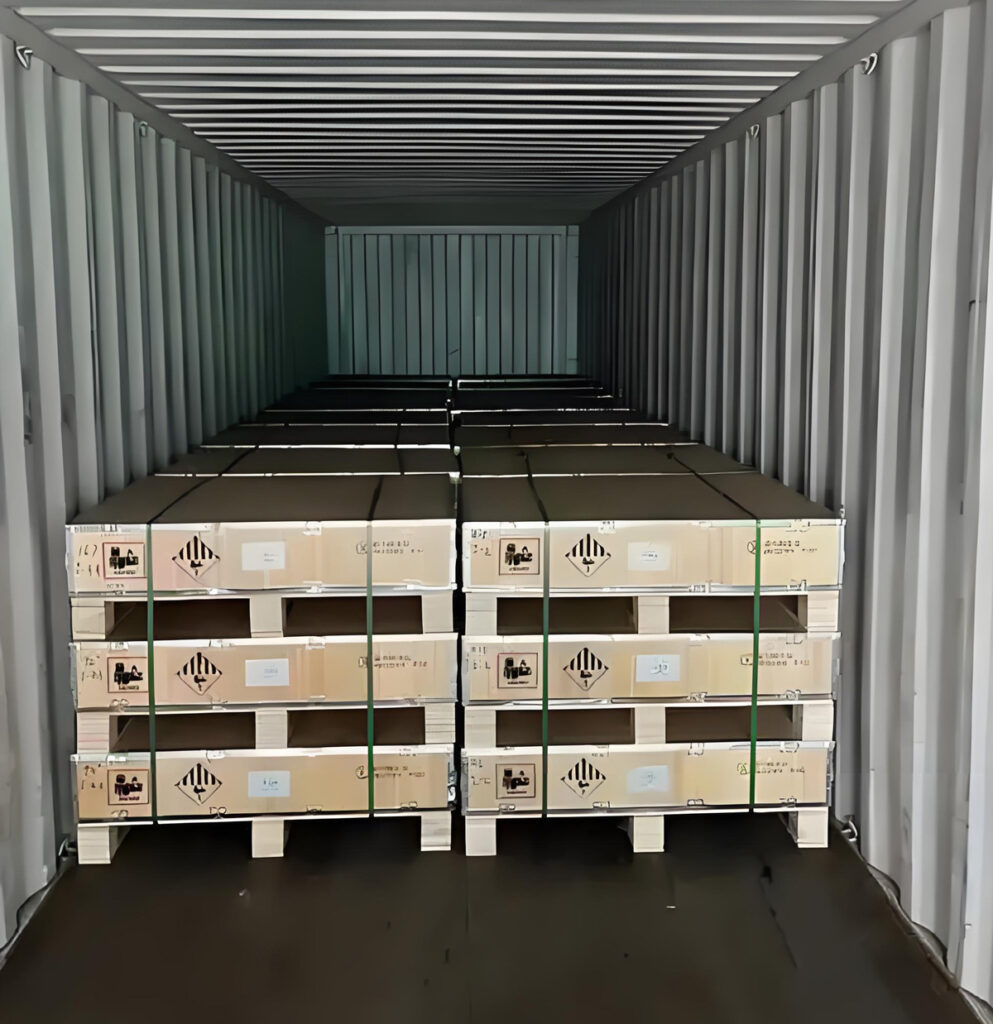
Risks of not entering the hazardous materials warehouse
If a company does not use the hazardous materials storage and does not meet the filing requirements, it may face:
- Customs inspection not passed, resulting in goods being detained or returned.
- Shipping company/airline refusal to accept, affecting booking and shipment.
- Risk of safety incidents, such as leaks, fires, or even explosions, leading to legal liability.
How to choose a hazardous materials warehouse ?
If a company needs installation in the hazardous materials warehouse, it is recommended to choose:
- Qualified hazardous materials warehouse (check its “Hazardous Goods Storage Business License”).
- Familiar with export declaration processes and able to assist in providing packing certificates, EDI declarations, and other services.
- Located close to the port, reducing transportation risks and costs.
Suggestions :
1. If the company has no experience in handling hazardous materials, it is strongly recommended to entrust a professional hazardous materials warehouse for packing to ensure compliant shipping.
2. If the company wishes to pack on its own, it should confirm qualification requirements in advance with the maritime bureau, freight forwarder, or customs broker to avoid delays or fines due to non-compliance.